Frequently Asked Foundation Repair Questions Phoenix, AZ
Frequently Asked Foundation Repair Questions Phoenix by Arizona Helical Piers, LLC 480-854-7661
The possibility of foundation failure in Arizona is something that everyone buying, selling, or occupying a home should consider. Foundation problems are commonplace, largely because soil conditions upon which residential and commercial buildings are constructed tend to be very unstable. Foundations are only as strong as the soil properties they are placed on. These soils are made up of thousands of years of sediments consist mainly of silts, clays and some granular soils. Also, Arizona has several large irrigated agricultural areas that have been turned into beautiful neighborhoods, most of which display evidence of foundation movement.
DO I HAVE A FOUNDATION PROBLEM?
The following check list of symptoms should help you identify serious foundation movement: (1) Inspect for cracks in brickwork/stem walls/footings. Look for previous patching. Look for separation between door, windows and brickwork. Also, check to see if chimneys or porches are moving away from the house or structure. (2) Look for cracks in interior wall of ceiling finishes and/or tearing of wallpaper, floor coverings, etc. (3) Check to see if windows or doors bind or stick or appear to be out of square. (4) Re-occurring leaks in ceilings, around chimneys, or increases in water bills.
If it is apparent that foundation failure has occurred, you should be aware that there are many different methods of repair available. They range greatly in cost, longevity, predictability and warranty.
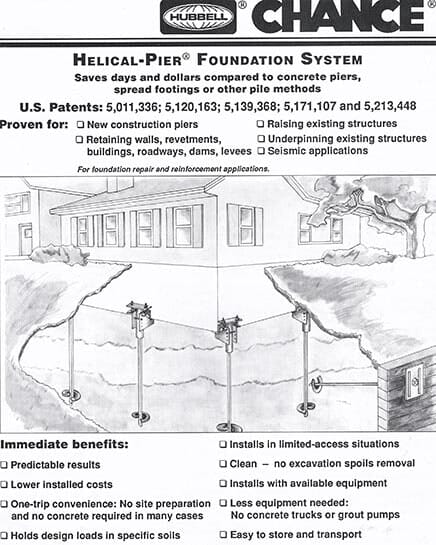
These methods are:
(a) Concrete Underpinning:
Shallow concrete pads placed less than 3 feet under existing foundation are used for additional support when settlement occurs. This method is costly, time consuming and offer only short lived stability as concrete pads are still bearing on unstable soils.
(b) Mud Jacking:
The injection of grout under higher pressure to raise slabs or foundations. Most commonly used to fill voids beneath slabs or leveling driveways, etc. Mud Jacking is moderately priced, however, it offers no stabilization value. The grout is bearing on top of the failed soils. It has no longevity. Also, it is crucial to understand that you are adding moisture to unstable soil in addition to a considerable amount of weight. In addition, in porous soils, the grouter can not control the flow of grout sometimes resulting in grout filled sewer systems, etc.
(c) Drilled Concrete Piers:
The boring of shafts to a depth of 9 to 12 feet, then filling them with concrete, used to offer additional support when settlement occurs, or to raise and level structures. Generally heavy external site disturbance with equipment and excavation and spoils removal. It is time consuming and unpredictable. Failure is possible if bearing on clays. It can actually be pushed up if placed in expansive soils. There are no guarantees and it is expensive.
(d) Driven Steel Piers:
The hydraulic advancement of steel sections of low-grade tubing, to rock or permanent bearing strata, used primarily to offer additional support when settlement occurs as well as to raise and level structures. Minimal site disturbance. This product is sold as inexpensive however; it is usually billed by the foot, which runs the cost up. With this hydraulic advancement system, no controls are given for tubing deflection, buckling or carry. It is leveraged by the building it is lifting (uses the buildings weight to push down pipes) and offers no safety factors for lifting and maintaining compressive loads. It relies mainly on skin fraction to support the structure. It offers longevity with no warranty to performance
(e) Chance Helical-Piers:
Helical piers are a slow-rotated, steel pier with various sized pitched plates that are installed below the existing foundation with minimal excavation, no spoils removal. Piers are constructed of high-strength 80ksi steel, connected with forged couplers as piers are advanced into a solid-bearing strata several feet below the active soil zones. Piers are installed using a pre-engineered, torque vs. capacity process that insures solid bearing for the compressive load demands of structure before structure weight is transferred to the installed piers. Special haunch brackets are attached to the existing foundation.
These piers are end bearing piers, meaning that all weight is transferred to the end of the pier, deep in stable bearing strata, and is not reliant on skin friction of the pier for support. This process is quick, cost effective, has minimal site disturbance and is a permanently guaranteed method for foundation repair. This system is the only system with ICBO (UBC) acceptance (ER-5110).
Foundation Repair Customer Testimonials Phoenix by Arizona Helical Piers, LLC 480-854-7661
Ivory, your crew as well as yourself performed wonderfully. The professionalism that was performed even impressed me ( I am not easily impressed). I hope you have a great X-Mas and hope your crew does as well.
Thank You,
Steve - GGS Specialty
Steve - GGS Specialty
Ivory,
I just spoke with a representative of Beazer Homes and was told that they were very pleased with your performance on this job. You were able to get it done without having to remove and concrete and that was very important to them. Getting this project done so quickly will surely provide you with many more opportunities with this client as they have many similar conditions across the valley.
Once again, thank you for a great job. I will send the invoice to the client first thing in the morning and will get you payment as soon as I can.
I just spoke with a representative of Beazer Homes and was told that they were very pleased with your performance on this job. You were able to get it done without having to remove and concrete and that was very important to them. Getting this project done so quickly will surely provide you with many more opportunities with this client as they have many similar conditions across the valley.
Once again, thank you for a great job. I will send the invoice to the client first thing in the morning and will get you payment as soon as I can.
Thank You,
Dr. Peter Fleming P.E. - Geotechnical Testing & Inspection
Dr. Peter Fleming P.E. - Geotechnical Testing & Inspection
Thank your staff for their professionalism, they did a great job!
Matthew Duran, Director Tuba City Regional Health
I wanted to take this opportunity to thank you and your team who did an excellent job of installation and coordination of helical piers. I must admit I had my doubts at first, but now believe after an excellent perfromance, you run a top notch company.
Thanks,
Ben Zwick - Whiting - Turner Contracting, Co.
Ben Zwick - Whiting - Turner Contracting, Co.
Frequently Asked Foundation Repair Questions Phoenix, AZ
Frequently Asked Foundation Repair Questions Phoenix by Arizona Helical Piers, LLC 480-854-7661
The possibility of foundation failure in Arizona is something that everyone buying, selling, or occupying a home should consider. Foundation problems are commonplace, largely because soil conditions upon which residential and commercial buildings are constructed tend to be very unstable. Foundations are only as strong as the soil properties they are placed on. These soils are made up of thousands of years of sediments consist mainly of silts, clays and some granular soils. Also, Arizona has several large irrigated agricultural areas that have been turned into beautiful neighborhoods, most of which display evidence of foundation movement.
DO I HAVE A FOUNDATION PROBLEM?
The following check list of symptoms should help you identify serious foundation movement: (1) Inspect for cracks in brickwork/stem walls/footings. Look for previous patching. Look for separation between door, windows and brickwork. Also, check to see if chimneys or porches are moving away from the house or structure. (2) Look for cracks in interior wall of ceiling finishes and/or tearing of wallpaper, floor coverings, etc. (3) Check to see if windows or doors bind or stick or appear to be out of square. (4) Re-occurring leaks in ceilings, around chimneys, or increases in water bills.
If it is apparent that foundation failure has occurred, you should be aware that there are many different methods of repair available. They range greatly in cost, longevity, predictability and warranty.
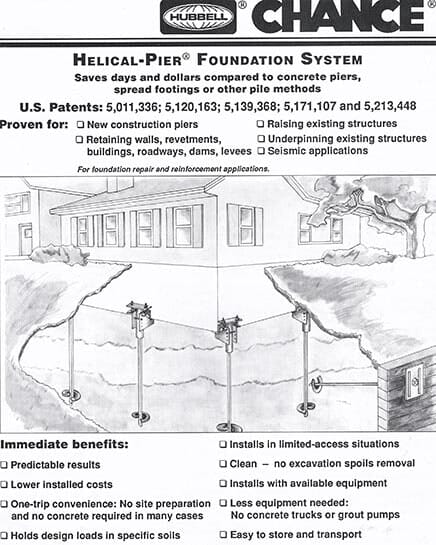
These methods are:
(a) Concrete Underpinning:
Shallow concrete pads placed less than 3 feet under existing foundation are used for additional support when settlement occurs. This method is costly, time consuming and offer only short lived stability as concrete pads are still bearing on unstable soils.
(b) Mud Jacking:
The injection of grout under higher pressure to raise slabs or foundations. Most commonly used to fill voids beneath slabs or leveling driveways, etc. Mud Jacking is moderately priced, however, it offers no stabilization value. The grout is bearing on top of the failed soils. It has no longevity. Also, it is crucial to understand that you are adding moisture to unstable soil in addition to a considerable amount of weight. In addition, in porous soils, the grouter can not control the flow of grout sometimes resulting in grout filled sewer systems, etc.
(c) Drilled Concrete Piers:
The boring of shafts to a depth of 9 to 12 feet, then filling them with concrete, used to offer additional support when settlement occurs, or to raise and level structures. Generally heavy external site disturbance with equipment and excavation and spoils removal. It is time consuming and unpredictable. Failure is possible if bearing on clays. It can actually be pushed up if placed in expansive soils. There are no guarantees and it is expensive.
(d) Driven Steel Piers:
The hydraulic advancement of steel sections of low-grade tubing, to rock or permanent bearing strata, used primarily to offer additional support when settlement occurs as well as to raise and level structures. Minimal site disturbance. This product is sold as inexpensive however; it is usually billed by the foot, which runs the cost up. With this hydraulic advancement system, no controls are given for tubing deflection, buckling or carry. It is leveraged by the building it is lifting (uses the buildings weight to push down pipes) and offers no safety factors for lifting and maintaining compressive loads. It relies mainly on skin fraction to support the structure. It offers longevity with no warranty to performance
(e) Chance Helical-Piers:
Helical piers are a slow-rotated, steel pier with various sized pitched plates that are installed below the existing foundation with minimal excavation, no spoils removal. Piers are constructed of high-strength 80ksi steel, connected with forged couplers as piers are advanced into a solid-bearing strata several feet below the active soil zones. Piers are installed using a pre-engineered, torque vs. capacity process that insures solid bearing for the compressive load demands of structure before structure weight is transferred to the installed piers. Special haunch brackets are attached to the existing foundation.
These piers are end bearing piers, meaning that all weight is transferred to the end of the pier, deep in stable bearing strata, and is not reliant on skin friction of the pier for support. This process is quick, cost effective, has minimal site disturbance and is a permanently guaranteed method for foundation repair. This system is the only system with ICBO (UBC) acceptance (ER-5110).
Foundation Repair Customer Testimonials Phoenix by Arizona Helical Piers, LLC 480-854-7661
Ivory, your crew as well as yourself performed wonderfully. The professionalism that was performed even impressed me ( I am not easily impressed). I hope you have a great X-Mas and hope your crew does as well.
Thank You,
Steve - GGS Specialty
Steve - GGS Specialty
Ivory,
I just spoke with a representative of Beazer Homes and was told that they were very pleased with your performance on this job. You were able to get it done without having to remove and concrete and that was very important to them. Getting this project done so quickly will surely provide you with many more opportunities with this client as they have many similar conditions across the valley.
Once again, thank you for a great job. I will send the invoice to the client first thing in the morning and will get you payment as soon as I can.
I just spoke with a representative of Beazer Homes and was told that they were very pleased with your performance on this job. You were able to get it done without having to remove and concrete and that was very important to them. Getting this project done so quickly will surely provide you with many more opportunities with this client as they have many similar conditions across the valley.
Once again, thank you for a great job. I will send the invoice to the client first thing in the morning and will get you payment as soon as I can.
Thank You,
Dr. Peter Fleming P.E. - Geotechnical Testing & Inspection
Dr. Peter Fleming P.E. - Geotechnical Testing & Inspection
Thank your staff for their professionalism, they did a great job!
Matthew Duran, Director Tuba City Regional Health
I wanted to take this opportunity to thank you and your team who did an excellent job of installation and coordination of helical piers. I must admit I had my doubts at first, but now believe after an excellent perfromance, you run a top notch company.
Thanks,
Ben Zwick - Whiting - Turner Contracting, Co.
Ben Zwick - Whiting - Turner Contracting, Co.